Chimico-Fisiche
Densità con ISO 1183-1 (cod. E.1)
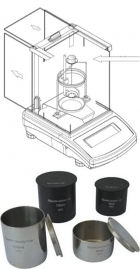
La densità relativa di polimeri non espansi si determina secondo la norma ISO 1183 parte 1 : «Metodo ad immersione con bilancia e picnometro per liquidi».
Secondo questo metodo si utilizza:
(cod. E.1B) i) una bilancia ad immersione con apposito dispositivo nel caso di liquidi con densità superiore o inferiore a quella dell'acqua a 23°C (metodo A equivalente alla procedura indicata dalla ASTM D 792);
(cod. E.1C) ii) un picnometro per liquidi con metodo ISO 2811-1, che utilizza una tazza in acciaio inox con volume definito di liquido di 50 ml, che garantisce una tolleranza di 0.1% (metodo B).
Densità apparente per polimeri in polvere (cod. E.1D)
La determinazione della densità apparente per polimeri in polvere si esegue con ASTM D 1895:
Parte A - comprende la misurazione di la densità apparente dei granuli e polveri fini che possono essere versato prontamente attraverso un piccolo imbuto.
Parte B - comprende la misurazione della densità apparente di materiali granulari, tra cui i pellets, che o non può essere versato attraverso l'imbuto descritto nel metodo di prova A.
Parte C - riguarda la misurazione della densità apparente di materiali forniti in forma di fiocchi, fibre corte o fili. Tali materiali non possono essere versato attraverso gli imbuti descritti metodi di prova in A e B. Inoltre, questi materiali normalmente sono molto ingombranti e comprimibili ad una massa minore per applicazione di un piccolo sforzo a compressione.
Misura della brillantezza (gloss) (cod. E.2)
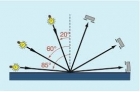
Determinazione della brillantezza (gloss) di rivestimenti polimerici (vernici) e lastre di polimeri termoplastici e termo-indurenti secondo le norme ISO 2813 e ASTM D 523-14, mediante strumento portatile MICROTRIGLOSS (interfaccia RS232 per computer e gestione dati con Software Easy-link in un intervallo da 0 a 180 GU con riproducibilità di 0,5 GU). Si applica a:
i) VERNICI MOLTO BRILLANTI con angolo di misura 20°
ii) VERNICI PIU' COMUNI con angolo di misura 60°
iii) VERNICI MOLTO OPACHE con angolo di misura 85°.
Misura della trasparenza (Haze)(cod. E.3)
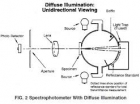
La determinazione della trasparenza (haze) di film polimerici è definita da norma ASTM D1003-13. La velatura (haze) può essere dovuta a:
i) tipo di pigmento e relativo grado di dispersione
ii) leganti usati o additivi
iii) trattamenti superficiali.
Misura del colore (cod. E.4)
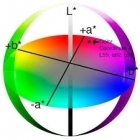
La determinazione delle coordinate di colore CIELab con metodi ASTM D 2244, E 308 e E 1164 è ottenuta con uno spettrofotometro da banco con sfera integratrice rivestita con un particolare strato di materiale bianco, che illumina il campione con luce diffusa. Particolari dispositivi posti all'interno della sfera (diaframmi) impediscono alla luce di illuminare direttamente la superficie del campione. Gli illuminanti previsti per la superficie del campione sono sorgenti a luce diurana diffusa (D65), a incadenscenza (A) e a flurescenza (F2). La misurazione dell'intensità della luce è effettuata con un rivelatore (400-700 nm) con angolo di lettura di 8°, provvisto di tre filtri (observer) che simulano i tre fotoricettori della retina dell'occhio umano alla luce rossa, verde e blu (vedi figura). Il software per il controllo del colore è utilizzato per il controllo di qualità per misurare superfici direzionali e uniformi come pure su pellet e materiali in polvere.
Assorbimento di acqua e ritiro lineare (cod. E.5)
Con la norma ASTM D 2732 si determina il ritiro lineare indotto dal trattamento termico per immersione in liquidi simulanti, come il polietilenglicole, la glicerina e l'acqua, in un intervallo di temperature variabili tra 90° e 150°C. Si misurano film con dimensioni 10x10 cm immersi tra due reti metalliche in acciaio inox in un bagno termostatico (vedi figura).
Con la norma ASTM D 570 si determina la percentuale di acqua assorbita per pesata del materiale prima e dopo immersione per 24 ore a 23°C. Questa norma è particolarmente applicabile a:
i) fogli con dimensioni 60x60 cm e spessore 1 mm
ii) film lunghi 76.2 mm [3 in], larghi 25.4 mm [1 in] di spessore di 3.2 mm [1⁄8 in]
iii) barre a sezione circolare lunghe 25.4 mm [1 in] e con diametro massimo di 25.4 mm [1 in]
iv) tubi con lughezza massima di 76 mm [3 in] e un diametro interno di 25.4 mm [1 in].
Macinazione granuli (cod. E.6)
Macinazione di polimeri termoplastici e termoindurenti con mulino Retsch a coltelli con setaccio da 0.5, 1 e 2 mm.
Possibile anche macinazione in presenza di agente criogenico in proporzioni 1:2 (Cod. E.7).
Distribuzione granulometrica di polveri (cod.E.8)
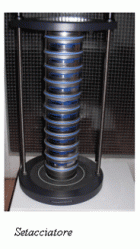
Determinazione della distribuzione media delle particelle di polimeri in polvere con setacciatore Retsch equipaggiato con 11 setacci a maglia quadrata con dimensioni variabile da 0.025 mm a 1 mm, come da norma ASTM D 1921.
Resistenza alla fiamma
Indice di ossigeno (cod. E.11)
Come definito dalla norma ISO 4589 (e parimenti dalla ASTM D 2863), l'indice limite di ossigeno (LOI) è la concentrazione minima di una miscela di ossigeno e azoto che - nelle condizioni di prova specificate - appena permette di mantenere la combustione di un materiale polimerico. Con un apposito strumento si misura la concentrazione relativa di ossigeno necessaria a bruciare un campione polimerico tenuto in modo verticale su una fiamma. Lo scopo di queste misure è quello di misurare la resistenza al fuoco (infiammabilità) durante la combustione del campione polimerico.
UL94 VB (cod. E.12)
Determinazione della resistenza al fuoco con metodo UL 94 Vertical Burning Test; determinazione della classe V-0, V-1, o V-2 in riferimento alle norme equivalenti ASTM D 3801 e ISO 1210 (oggi sostituita dalla IEC 60695–11–10/B).
UL94 VA (cod. E.13)
Determinazione della resistenza al fuoco con metodo UL 94 Vertical Burning Test; determinazione della classe 5VA o 5VB in riferimento alle norme equivalenti ASTM D 5048 e ISO 10351 (oggi sostituita dalla IEC 60695–11–20).
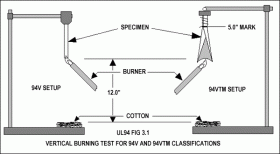
Termo-ossidazione in stufa termoventilata (cod. E.14)
Si eseguono prove di termo-ossidazione accelerata in stufa termoventilata e simulazioni di esposizione a cicli termici con controllo di temperatura e umidità relativa e di invecchiamento termo-ossidativo in camera climatica. Mediante le prove di invecchiamento accelerato è anche possibile caratterizzare i campioni prima e dopo i vari cicli eseguiti in condizioni controllate.
Prove in camera climatica (cod. E.15)
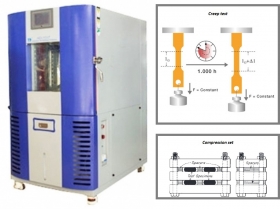
Si eseguono prove in camera climatica Haida International HD-150T a temperatura controllata da -50°C a +150°C e a umidità relativa da 55% a 90%RH, per valutare il comportamento di film, placchette e provini di varie dimensioni ottenuti sia da materiali termoplastici che termoindurenti.
In particolare si possono applicare cicli termici con controllo di temperatura e umidità relativa per il condizionamento di provini in particolari condizioni, per le successive prove meccaniche (come ad esempio trazione secondo ISO 527-2 o prove a impatto secondo ISO 179 a basse temperature).
In camera climatica si eseguono inoltre:
- Creep Test (cod. E.15A) a sforzo costante secondo la norma ISO 899-1. La norma specifica un metodo per determinare lo scorrimento a trazione delle materie plastiche in condizioni specificate come quelle di pretrattamento, temperatura e umidità. Il metodo è adatto per l'impiego con materiali plastici rigidi e semirigidi non rinforzati, caricati e rinforzati con fibre in forma di provini sagomati stampati direttamente o ricavati per lavorazione meccanica da lastre o articoli stampati. Il metodo prevede la determinazione dello scorrimento a trazione misurando le variazioni della distanza tra i morsetti. I materiali possono essere testati applicando una vasta gamma di sollecitazioni, tempi e condizioni ambientali.
- Prove di Compression Set (cod. E.15B) a determinate temperature secondo la norma ISO 815 metodo B (o ASTM D 395). Queste prove si applicano ad esempio a materiali destinati a condizioni d'uso che implicano sollecitazioni statiche ad elevate temperature. L'apparato strumentale costituito da una serie di lastre in acciaio e contenenti i provini, viene introdotto per un tempo predefinito in camera climatica, in condizioni di temperatura e umidità controllata. A ciclo ultimato si misura quindi la capacità del materiale di mantenere le proprietà elastiche dopo l’azione prolungata di sollecitazione in compressione.
ESCR (cod. E.16)
Le misure della resistenza a solventi o altri additivi (ESCR), saranno concordate con il committente secondo le norme ASTM D1693:2008 (Standard Test Method for Environmental Stress-Cracking of Ethylene Plastics) e ISO 16770:2004 (metodo per la determinazione della resistenza allo stress-cracking di polietilene in qualsiasi ambiente).
La rottura per effetto della fatica e di un agente chimico aggressivo per il polietilene è definita Environmental Stress Cracking Resistance (ESCR). Questo fenomeno dipende dall’esistenza di stress esterni poliassiali combinati con stress interni, fatta eccezione per polimeri altamente cristallini per i quali è sufficiente l’azione dei soli stress interni. L'ESCR di una struttura è tanto maggiore quanto più elevato è il peso molecolare e tanto più bassa la cristallinità. La presenza di una elevata quantità di bassi pesi molecolari può ridurre la resistenza all’ESCR. Poiché è difficile evidenziare gli stress derivanti dalla trasformazione e dall’invecchiamento si usano prove accelerate quali:
i) provino sottoposto a deformazione costante (Bell test - ISO 22088-5)
ii) provino sottoposto a stress costante (Lander test)
iii) test su flacone sottoposto a pressione interna costante (specifico per il soffiaggio).
Biodegradabilità EN ISO 13432 (cod. E.17)
La norma UNI EN 13432:2002 è una norma riportata nella Gazzetta Ufficiale delle Comunità Europee e pertanto deve essere recepita in Europa a livello degli Stati Membri e fornisce presunzione di conformità con la Direttiva Europea 94/62 EC, sugli imballaggi e rifiuti da imballaggio.
La norma definisce uno schema di prova e criteri di valutazione per l'accettazione finale degli imballaggi adottata anche in Italia, specificando i requisiti che deve possedere un materiale polimerico per poter essere definito compostabile.
Secondo la EN 13432:2002, le caratteristiche che un materiale compostabile deve avere sono le seguenti:
1. Biodegradabilità, determinata misurando l'effettiva conversione metabolica del materiale compostabile in anidride carbonica. Questa proprietà è valutata quantitativamente con il metodo di prova standard ISO 14855 con cui si determina la biodegradabilità attraverso le concentrazioni di anidride carbonica emessa relativamente al contenuto di carbonio totale.
2. Disintegrabilità, cioè la frammentazione e perdita di visibilità nel compost finale (assenza di contaminazione visiva).
3. Assenza di effetti negativi sul processo di compostaggio, requisito verificato con una prova di compostaggio su scala reale o pilota.
4. Bassi livelli di contaminazione: livello in metalli pesanti (al di sotto di valori massimi predefiniti) e assenza di effetti negativi sulla qualità del compost, accertabile con una prova di germinazione e crescita di piante (test OECD 208 modificato) eseguita su campioni di compost nei quali è avvenuta la degradazione del materiale di prova.
5. Altri parametri chimico-fisici possono essere valutati, che non devono differire dal compost di controllo dopo la biodegradazione sono: pH; contenuto salino; solidi volatili; contenuto di azoto e di metalli pesanti.
Prove di biodegradazione con metodo ISO 14855-1 (cod. E.18)
La UNI EN ISO 14855-1 riguarda la "Determinazione della biodegradabilità aerobica finale e della disintegrazione dei materiali plastici in condizioni controllate di compostaggio". La norma definisce una metodica che si applica in via generale per i “manufatti di plastica” ed è riconosciuta sia a livello Italiano che Europeo. Con questa norma si può eventualmente certificare che il manufatto in plastica è biodegradabile (con una percentuale che può variare dallo 0 al 100%) in funzione della CO2 netta prodotta a seguito della biodegradazione della plastica. Per validare la procedura areobica di biodegradazione è necessario usare come materiale di riferimento la cellulosa Avicel, che deve degradarsi in una percentuale maggiore del 70% in 45 giorni.
Le prove di biodegradabilità vengono realizzate in un Incubatore IC 400 Salvis Lab. Il flusso d'aria è regolato da un’elettrovalvola a 10 vie, per garantire le condizioni aerobiche previste dalla norma, e viene monitorato attraverso due flussimetri interfacciati al software di gestione LabVIEW. L’anidride carbonica prodotta viene misurata tramite un analizzatore IR di CO2, per determinare, nel tempo di compostaggio, i quantitativi di CO2 emessi durante la biodegradazione del materiale polimerico disperso nel compost derivante dalla frazione umida della raccolta differenziata.
Resistività di volume e superficie di materiali isolanti e conduttivi (cod.E.19)
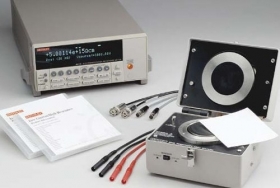
La resistività è una caratteristica fondamentale dei materiali polimerici e permette di determinare diverse proprietà:
i) la rigidità dielettrica di un materiale isolante, definita come il valore limite di campo elettrico oltre il quale si produce una conduzione di elettricità (scarica elettrica) attraverso il materiale polimerico con proprietà dielettriche;
ii) il fattore di dissipazione, utilizzato per valutare ad esempio le perdite dielettriche dei cavi;
iii) la continuità meccanica;
iv) il contenuto di umidità;
v) la conducibilità elettrica di materiali plastici conduttivi, caricati con nanotubi di carbonio, grafene e nero fumo conduttivo al fine di ridurre le cariche elettrostatiche superficiali.
Nel Sistema Internazionale, la resistività di volume è numericamente uguale alla resistenza in corrente continua tra le facce opposte di un materiale con volume pari a un metro cubo (espressa in Ohm·cm).
La resistività superficiale è invece la resistenza opposta al passaggio di corrente lungo la superficie del materiale, ed è indipendente dalle dimensioni fisiche del campione (espressa in Ohm).
Nello specifico, le misure di resistività di volume e superficie vengono condotte in conformità alle norme ASTM D-257 e IEC 60093 per i materiali isolanti, e ISO 3915 per i materiali conduttivi, impiegando un elettrometro Keithley 6517A e una cella per misure di resistività Keithley 6105.
Il metodo prevede l’applicazione di una tensione nota V, e la misura della corrente elettrica I risultante dopo un periodo di elettrificazione di 60 secondi. Lo strumento calcola quindi la resistenza R applicando la legge di Ohm (R = V/I), e la resistività ρ, determinata in base alla geometria dei provini e alla temperatura di prova.
Per i test si utilizzano generalmente lastrine di dimensioni 100x100 mm di spessore 3 mm. Mentre le tensioni applicate vanno da 1 V per materiali conduttivi, fino a 500 V per materiali isolanti.